Fusión flash
La fusión flash es un proceso de extracción pirometalúrgica de metales no ferrosos, que consiste en oxidar y fundir simultáneamente los metales contenidos en una mena sulfurosa, como la calcopirita. El proceso fue inventado por la empresa finlandesa Outokumpu, siendo utilizado desde 1949 para la metalurgia del cobre. Desde entonces, se ha adaptado a la extracción de níquel y plomo. Al comienzo de siglo XXI, la fundición flash participa en el 50 % de la producción mundial de cobre, el 30 % de la producción de níquel[1] y el 10 % de la producción de plomo.[2]
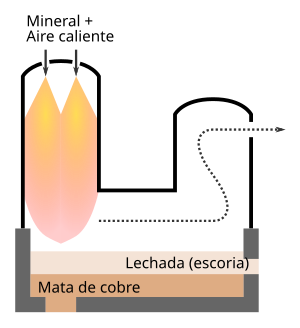
Historia
editarFin del siglo XIX: primeros intentos
editarLa idea de oxidar el azufre contenido en los minerales de cobre sulfurosos es antigua. En la década de 1870, el metalúrgico inglés John M. Hollway experimentó con la fusión y el afinado del cobre mediante un convertidor inspirado en el convertidor Bessemer. Propuso el sulfuro de hierro como combustible, generando su oxidación para formar SO
2 y una escoria de FeO. Sin embargo, la oxidación no es completa: Hollway se preocupó de tener siempre un exceso de azufre en el baño de material fundido para evitar la oxidación del cobre, pero también del níquel y de los metales preciosos que generalmente acompañan al cobre en pequeñas proporciones, como la plata o el oro.[3]
Por lo tanto, Hollway estaba considerando la producción de una mata blanca, es decir, una mezcla de cobre y azufre, pero no planeó llevar la refinación más allá para eliminar todo el azufre.[4] Comenzó una serie de extensos experimentos a mediados de la década de 1870 en Penistone, en Inglaterra,[5] convirtiéndose en el pionero de los intentos de fundir y refinar piritas cupríferas en un solo paso.[6] A pesar de su perseverancia, Hollway no logró desarrollar un proceso utilizable industrialmente:
En este año [1878], Hollway sugirió y experimentó con el principio que había señalado, sentando las bases para la refinación de las piritas y su actual conversión. El aire se soplaba a través de unas piritas de Río Tinto en un convertidor Bessemer ordinario y el experimento fue un éxito notable. Sin embargo, el aparato era inadecuado y el proceso funcionaba de forma muy intermitente y se producían grandes cantidades de escoria, que había que vaciar regularmente, mientras que la posición de las boquillas de este convertidor resultó insatisfactoria. […] En la forma final del aparato de Hollway para fundir piritas de mineral a metal, la introducción de silicio como fundente para el óxido de hierro, combinado con el uso de un refractario básico, pretendía resolver las dificultades relacionadas con el ataque experimentado por el revestimiento refractario silíceo.[7]Donald M. Levy; (Modern copper smelting)
Sin embargo, sin ocultar nada de sus fracasos y publicando patentes sin futuro,[nota 1] Hollway hizo públicos en detalle sus pruebas y sus resultados. Por lo tanto, cuando Pierre Manhès y Paul David desarrollaron el proceso Manhès-David, su invento se benefició inmediatamente de la experiencia adquirida en las pruebas de Hollway. Pero su proceso se limitaba al refinado mediante el insuflado de aire en una mata previamente fundida.
Primera mitad de siglo XX: procesos específicos
editarEn 1898, el metalúrgico estadounidense Edward Dyer Peters calculó que el 60 % del costo de producción del cobre correspondía al consumo de combustible. A ningún metalúrgico se le escapaba que este combustible se utilizaba para eliminar el hierro y el azufre combinados con el cobre. Sin embargo, estos elementos en sí mismos podrían ser combustibles útiles. En particular, el tostado de minerales es una operación[8] de desulfuración que requiere un uso intensivo de combustible.
El uso de un alto horno para la fusión de pirita de cobre se probó ya en 1878. El coque iniciaba la combustión del azufre contenido en el mineral. Gracias a la excelente eficiencia del alto horno,[nota 2] era posible obtener una reducción del 40 % en los costos de combustible. Además, se evitaban las etapas de trituración y de tostación del mineral, que representaban entonces entre el 17 % y el 50 % del costo de transformación del mineral en cobre. Pero la fundición en altos hornos también tiene sus inconvenientes, porque es efectivo solo con minerales suficientemente ricos y de naturaleza rocosa; y los yacimientos metalíferos de este tipo ya estaban casi todos agotados en la década de 1930. Estos hornos también eran difíciles de operar y producían una mata de baja calidad.[8][nota 3]
El uso de un horno de reverbero también permite la fusión y el refinado simultáneos de piritas, y en 1878 el metalúrgico estadounidense Henry L. Bridgman patentó su principio de funcionamiento,[10] que consistía en oxidar el mineral sulfuroso una vez pulverizado finamente. Si bien los procesos de enriquecimiento que se comenzaron a desarrollar (como la flotación por espuma), facilitaban la producción de dicho mineral, la idea no se materializó. Además, la baja eficiencia de los hornos de reverbero hizo que todo el proceso solo permitiera una reducción del 5 % del combustible necesario.[8] En 1915, investigadores de la compañía Anaconda Copper patentaron el uso de un regenerador Siemens para mejorar su eficiencia térmica.[11] Pero no hay constancia de que su invento, al igual que el similar patentado en 1932 por Horace Freeman,[12] llegara a ser materializado.[8]
Basándose en estas patentes, algunos investigadores que daban por sentada la teoría de la oxidación de la pirita, comenzaron a trabajar en su puesta en práctica a escala industrial. En la década de 1930, Frederick Laist y J. P. Cooper, todavía de Anaconda Copper, demostraron que recuperar el calor liberado por la oxidación de piritas durante su tostado sobre solera giratoria podía ahorrar hasta un 60 % del combustible necesario para la operación. En 1935 se evaluó un horno similar en la Unión Soviética, que se abandonaría poco después debido al mal resultado de los refractarios y a la obstrucción del horno causada por partículas fundidas. En 1937, la Société française des mines de Bor probó un horno vertical, pero abandonó sus pruebas debido a dificultades técnicas, y especialmente por el inicio de la Segunda Guerra Mundial.[8]
Finalmente, en 1936, Telfer E. Norman, un metalúrgico que trabajaba en nombre de la compañía Inco, publicó una revisión exhaustiva sobre el tema de la fusión de pirita sin combustible. Demostró que el calor desprendido por la oxidación de las piritas no es suficiente para la fusión: el calentamiento del nitrógeno del aire utilizado para oxidar las piritas consumía demasiado calor. Sin embargo, en una atmósfera que contuviese más del 40% de oxígeno, la fusión de un mineral sulfuroso muy concentrado se volvía teóricamente posible. Dado que, en ese momento, las técnicas criogénicas para producir oxígeno puro se volvieron bastante viables para aplicaciones industriales, no existía ningún impedimento teórico o tecnológico para el desarrollo de un proceso de fusión autógena para las piritas:[8]
Siempre que se pueda desarrollar un horno adecuado y demuestre ser una herramienta [industrialmente] satisfactoria, el parámetro que se vuelve más importante sería el costo relativo del combustible y del oxígeno.[13].J. Newton & C. L. Wilson; (Metallurgy of Copper)
Sin embargo, la llegada de la Segunda Guerra Mundial supuso que se suspendieran todas las investigaciones.
Década de 1950: desarrollo del proceso
editarOutokumpu
editarEn 1936, la pequeña empresa finlandesa Outokumpu, fundada en 1914 cerca de la localidad epónima para explotar un depósito de cobre local, encargó una horno de arco eléctrico para la fundición del mineral en mata. Este horno era entonces el más grande del mundo para este uso. Pero, en 1944, el Armisticio de Moscú dio lugar a la anexión por parte de la Unión Soviética de la región finlandesa de Carelia, y por lo tanto de las dos represas hidroeléctricas de Enso-Vallinkoski y de Lesogorsk/Rouhiala, privando al mismo tiempo a Finlandia de un tercio de su capacidad de producción de electricidad. Este hecho, combinado con la desmovilización y el pago de reparaciones de guerra (el 61 % de las exportaciones del país en 1945) supuso una gran presión sobre la industria finlandesa. Mientras la empresa Outokumpu consumía el 3% de la electricidad del país, el precio de esta energía se quintuplicó entre 1946 y 1948.[8]
Pero, ya en 1945, anticipándose a las fuertes restricciones que estaba sufriendo el suministro eléctrico, la empresa se embarcó en el estudio del desarrollo de un proceso más eficiente energéticamente. En tan solo tres meses, el equipo de cuatro ingenieros encargado de solucionar el problema ideó una alternativa. Sus cálculos demostraron que oxidando el mineral concentrado con aire, y luego recuperando el calor de los humos para precalentar el aire oxidante, era posible lograr la fusión casi sin agregar combustible. En febrero de 1947, menos de dos años después del inicio de los estudios, ya estaba operativo el antecesor de los hornos de fusión flash. Se construyó un modelo industrial a partir de septiembre,[nota 4] que comenzó a operar tres meses después. En 1949, el proceso estaba operativo en la fábrica de Harjavalta, aunque el horno eléctrico de antes de la guerra todavía aseguró un tercio de la producción de Outokumpu hasta 1953.[8]
Inco
editarDespués de la Segunda Guerra Mundial, el gigante mundial de níquel, la empresa canadiense Inco[nota 5] reanudó la investigación donde Norman se había detenido. Con abundante electricidad gracias a la explotación de las cataratas del Niágara, y uniéndose a la francesa Air Liquide, una empresa más pequeña pero mucho más agresiva[nota 6] que su competidora Linde, Inco retomó el desarrollo de un horno de fundición flash mediante enriquecimiento con oxígeno. El prototipo se comenzó en enero de 1947 (es decir, un mes antes que el de Outokumpu), pero el primer modelo industrial operativo solo estuvo listo el 2 de enero de 1952.[8] Al igual que su equivalente Outokumpu, es una evolución directa del horno de reverbero.[14]
Aunque el horno flash de Inco no tenía el propósito de ahorrar energía como el de Outokumpu, demostró ser térmicamente más eficiente. De hecho, los intercambiadores de calor elegidos por Outokumpu son menos sofisticados que los de tecnología criogénica utilizados por Inco. También son más frágiles y menos eficientes.[8]
La ausencia de nitrógeno en el aire comburente genera humos muy ricos en SO
2 (aproximadamente un 50%), lo que simplifica considerablemente su tratamiento. Así, en 1952, el primer horno industrial de Inco estaba asociado a una unidad de tratamiento de tamaño estándar, mientras que eliminaba diez veces más azufre que cualquier otra unidad equivalente en el mundo.[14]
Hornos flash
editarHorno flash de Outokumpu
editarAunque menos eficiente que el diseño de Inco, el horno de Outokumpu acabó imponiéndose. De hecho, la empresa finlandesa adoptó una estrategia de venta de sus patentes y exportación de su procedimiento que permitió la rápida difusión de su tecnología. Por el contrario, Inco solo utilizó fundición flash para mantener su cuasi-monopolio en la producción de níquel.[8]
El horno de Outokumpu consta de un cilindro vertical, el reactor, por cuya parte superior entra el mineral concentrado seco y pulverizado, y el aire, posiblemente mezclado con oxígeno, combustible o un fundente silíceo. Llevado instantáneamente a alta temperatura, el concentrado se oxida y funde durante su caída en el reactor. Luego llega a la cámara de sedimentación, donde se separan la mata y la lechada. Los humos escapan por el otro extremo de la cámara a través de un conducto vertical, que los lleva a un recuperador de calor. En Harjavalta, un concentrado de cobre al 23 % da una mata de cobre al 64 % y genera entre un 11 y un 14 % de SO
2. En 1996, el horno flash más grande de este tipo, instalado en San Manuel (Arizona), produjo 1,2 Mtm/año de mata e incluso podría haber alcanzado 2 Mtm/año con algunas modificaciones. En comparación con un horno de reverbero, la producción es 4 veces mayor para una superficie igual, y el consumo de energía se divide por 2.[15]
Originalmente, el precalentamiento del aire a una temperatura de entre 200 y 800 °C permitía lograr un funcionamiento autógeno.[16] En 1971, Outokumpu adoptó el enriquecimiento de oxígeno en su planta de Harjavalta.[1] Esta actualización lleva el horno de Outokumpu al mismo nivel de eficiencia energética que el de Inco[8] Al comienzo de siglo XXI, el enriquecimiento de oxígeno, a niveles de entre el 30 y el 90 %, reemplazó casi en todas partes a la recuperación de calor.[16]
En 1978, el horno flash instalado en Głogów (Polonia), logró por primera vez realizar una fusión flash suficientemente oxidante para producir blister, es decir, cobre metálico con algunas impurezas, en lugar de mata, haciendo innecesario el paso del afinado de la mata realizado por el proceso Manhès-David en un convertidor Peirce-Smith. La fundición de Olympic Dam (Australia), también adoptó este proceso en 1988. Al comienzo del siglo XXI, la fundición flash de mineral para obtener blister solo está operativa en estas dos plantas.[1]
Este horno también se utilizó para la producción de plomo y para recuperar los residuos de jarosita (un sulfato de hierro y potasio).[16] Uno de sus principales inconvenientes es su incapacidad para fundir los residuos de cobre.[E 1]
Al comienzo del siglo XXI, un horno flash grande de Outokumpu normalmente mide interiormente 20 m de largo, 7 m de ancho y 2 m de alto. Su interior está revestido con ladrillos refractarios de magnesita-cromo, enfriados por una camisa de agua. Dicho horno transforma diariamente 3000 tm de concentrados en 1500 tm de mata y otras tantas escorias, utilizando aire enriquecido con el 50-80% de oxígeno. Puede funcionar ininterrumpidamente durante más de 8 años sin mayores reparaciones de su revestimiento refractario interno.[E 2]
Horno flash de Inco
editarEl horno de Inco consiste en introducir por boquillas laterales el mineral concentrado pulverizado mezclado con fundentes. Transportado por el oxígeno, el mineral entra a la cámara de combustión donde se enciende instantáneamente. Los humos son evacuados a través de una chimenea central. En 1996, en la planta de Copper Cliff, un horno de Inco[15] produjo una mata de cobre-níquel al 45 %, una escoria de Cu-Ni al 0,75 % y un humo con SO
2 al 75 %.
El funcionamiento con oxígeno puro genera humos muy ricos en SO
2 (del 55 al 75 % de SO
2, frente al 1 % de un horno de reverbero),[E 3] lo que facilita su reprocesamiento: la unidad de tratamiento de humos es 10 veces más pequeña que la de un horno de reverbero de la misma capacidad. Además, la recuperación de calor es más fácil debido al bajo volumen de humos.[nota 7][14]
En 2011, la fundición flash aseguró las tres cuartas partes de la producción de níquel extraído de minerales sulfurosos (los minerales de níquel tipo saprolito se funden en un horno eléctrico). Hay 9 hornos de fusión flash dedicados a la producción de níquel: 7 hornos tipo Outotec que proporcionan el 70% de la fusión flash de níquel y 2 hornos tipo Inco que producen el 30% restante.[17]
Al principio del siglo XXI, un horno flash grande de Inco normalmente mide interiormente 22 m de largo, 5,5 m de ancho y 5 m de alto. Su interior está revestido con ladrillos refractarios de magnesita-cromo, enfriados por una camisa de agua. Dicho horno transforma diariamente 1800 tm de concentrados en 1000 tm de mata y 1200 tm de escoria, consumiendo 450 tm de oxígeno puro. Puede operar durante 5 a 6 años sin reparaciones importantes en su revestimiento refractario interno.[E 4]
Horno flash Kivcet
editarDirectamente derivado del horno de Outokumpu,[16] el horno Kivcet fue desarrollado en 1967 por el Instituto soviético VNIITSVETMET en Öskemen, Kazajistán, bajo la dirección del profesor A. P. Sychev. En 1985, se instaló la primera unidad industrial para la producción de plomo y zinc en el kombinat de Öskemen (ahora Kazzinc).[18] En su primera versión, la cámara de reacción estaba ubicada en el centro del horno, y las partículas allí estaban animadas por un movimiento ciclónico. A continuación, los materiales fundidos se proyectaban contra la pared, fluyendo sobre ella. Pero el PbO corroe el revestimiento del refractario, por lo que se abandonó esta disposición para dar lugar al diseño actual, en el que la cámara de reacción está separada del horno de arco eléctrico.[2]
La cámara de combustión es un horno flash clásico que utiliza oxígeno puro. La oxidación de los sulfuros es suficientemente exotérmica como para provocar su fusión. Pero antes de llegar al fondo de la cámara de decantación, los óxidos fundidos atraviesan una capa de coque a más 1200 °C que, a tales temperaturas, arde liberando un gas altamente reductor, monóxido de carbono. Así, los óxidos fundidos sufren una reducción hasta alcanzar su estado metálico. Esta reducción, así como la separación por decantación entre el metal y la escoria, se completa en el horno eléctrico, cuyos electrodos mantienen los materiales en fusión.[2]
En 2004, el proceso Kivcet representó el 10% de la capacidad de producción mundial de plomo (estimada en 3,54 Mtm/año).[2] El proceso también se utiliza para la producción de cobre.[16]
El proceso
editarPrincipio
editarEl propósito principal de un horno flash es fundir un concentrado de mineral, que generalmente contiene 30-40% de cobre[E 5] o 12-20% de níquel.[17] La temperatura que allí se alcanza, 1250 °C, permite tener una mata y una escoria en fusión, y suficientemente fluidos para disociarlas por decantación.[E 5]
El mineral concentrado debe pulverizarse finamente (a un tamaño de 100 μm) y secarse para que se encienda. Los concentrados de flotación por espuma suelen tener este tamaño.[E 5]
Los productos resultantes de la fusión flash son:[E 5]
- Mata fundida: en el caso de la metalurgia extractiva del cobre, el contenido del metal suele alcanzar el 65 % o el 40 % de níquel en el caso de la extracción del níquel
- Lechada: su contenido en sílice permite estabilizar óxido de hierro FeO en forma de fayalita Fe
2SiO
4. Contiene del 1 al 2 % de cobre o níquel - Humo: contiene, según el nivel de enriquecimiento de oxígeno, del 30 al 70 % de SO
2. El horno de Inco, que funciona con oxígeno puro, produce humo con un 75 % de SO
2.
Los procesos en los hornos de Outokumpu e Inco son muy similares. La comparación de sus respectivas ventajas y desventajas es frecuente. El éxito de los hornos de Outokumpu se puede atribuir a la estrategia de la empresa, pero también a su sencillez (un solo quemador), así como a la mayor distancia entre el quemador y la salida de humos que favorece el intercambio de calor. La recuperación de energía del horno Outokumpu es más relevante que la de los hornos Inco, que producen grandes cantidades de vapor para el que hay que encontrar una utilidad. Pero la configuración horizontal de los hornos de Inco favorece la decantación de la escoria, que así restituye casi todo el cobre y el níquel a la mata.[E 6]
Reacciones químicas
editarUna fundición flash realiza simultáneamente tostado (es decir, la oxidación del mineral que permanece en estado sólido), fundición y refinación de la mata de cobre.[17]
- Metalurgia extractiva del cobre:
- En el caso de la fusión de calcopirita (de fórmula estructural CuFeS
2), la principal reacción es:
- 2 CuFeS
2(s) + O
2(g) → Cu
2S. FeS (l) + FeO (l) + SO(g)
2 producen 450 kJ/mol de CuFeS
2[E 7]
- Metalurgia extractiva del níquel:
- En el caso de la fusión de la pentlandita (de fórmula estructural (Fe,Ni)
9S
8), la principal reacción es:
- (Fe,Ni)
9S
8(s) + O
2(g) → NiS (l) + FeO (l) + SO(g)
2 producen 1200 kJ/mol de (Fe,Ni)
9S
8[17]
- Metalurgia extractiva del plomo:
- En el caso de la fusión de galena (de fórmula estructural PbS), las reacciones que dominan son:
- PbS (s) + O
2(g) → Pb (l) + SO(g)
2 producen 219 kJ/mol de PbS
- Pb (l) + O
2(g) → PbO (l) + SO(g)
2 producen 298 kJ/mol de PbS - PbS (l) + 2 PbO (l) → 3 Pb (l) + SO(g)
2 producen 61 kJ/mol de PbS
- Cuando la relación O
2/PbS se elige correctamente, una parte significativa de la galena PbS se oxida a plomo metálico. Pero la escoria contiene entre un 30 y un 40 % de litargirio (PbO), que no es despreciable, aunque la cantidad de escoria sea bastante baja (una tonelada de escoria por tonelada de concentrado).[19] Para no perderse con la escoria, el litargirio debe reducirse en CO. Esta reducción siendo imposible en el medio oxidante necesario para la fusión flash, se hace en el horno eléctrico relacionado, que se comunica con el horno flash por un sifón:
- C (s) + CO
2(g) → 2 CO (g) consumen 165,4 kJ/mol de CO - PbO (s) + CO (g) → Pb (l) + CO(g)
2 producen 95,8 kJ/mol de PbO
- El equilibrio térmico de estas dos reacciones es deficitario: entonces es necesario proporcionar calor mediante un horno eléctrico.[2]
- Reacciones relacionadas:
- La pirita y la pirrotina (de fórmulas FeS
2 y Fe
8S
9) presentes en los minerales sulfurados se tuestan y funden según reacciones muy exotérmicas:
- Fe
8S
9(s) + O
2(g) → FeO (l) + 2 SO(g)
2 producen 700 kJ/mol de FeS
2[20]
- Fe
8S
9(s) + 13 O
2(g) → 8 FeO (l) + 9 SO(g)
2 producen 2500 kJ/mol de Fe
8S
9[17]
- El óxido de hierro FeO, producido por las reacciones anteriores, es un elemento de la escoria. A las temperaturas presentes en el horno, se combina con sílice (SiO
2), que servirá como fundente:[nota 8]
- Las primeras reacciones de tostado son suficientemente exotérmicas como para fundir el mineral concentrado. Sin embargo, sucede que se añaden quemadores adicionales, para limitar el consumo de oxígeno, o para fundir residuos de cobre que no se combinan con el azufre.[E 9] Si la oxidación del hierro en FeO es exotérmica, la transformación del FeO resultante en Fe
2SiO
4 implica la adición de sílice, que se coloca en un horno frío. El balance general es desventajoso porque el calor desprendido por las reacciones químicas no compensa el necesario para calentar la sílice: se evita tratar minerales concentrados ricos en hierro, y solo se introduce la cantidad de sílice estrictamente necesaria. Por lo general, la cantidad de sílice se limita buscando una relación SiO
2/Fe de entre 0,7 y 1.[E 10]
Desarrollos actuales y futuros
editarLa fusión flash a menudo se cita como una tecnología disruptiva, una de las más destacadas de siglo XX.[8] Este proceso autógeno, sustituye tanto a los hornos de reverbero, caracterizados por su mediocre rendimiento térmico, como a los hornos de tostación, que no aprovechan el calor que desprende la operación. Además, el humo de estos hornos es una mezcla de humo de combustión con el de la reacción de oxidación. Por tanto, sus humos son menos ricos en azufre y la desulfuración es más difícil: el 98,5% del azufre emitido por los hornos flash se recupera, mientras que la recuperación solo alcanza el 40% en los hornos de reverbero. Los hornos de reverbero emiten 1926 kg de CO
2 y 963 kg de azufre por tonelada de cobre, mientras que las emisiones de los hornos flash son, respectivamente, 46 kg y 23 kg.[24]
La principal desventaja de la fundición flash es su atmósfera altamente oxidante, que oxida los metales que se desean recuperar. La escoria es más rica en óxidos de níquel, cobre o plomo, y conviene calentarla en un horno eléctrico donde, mezclada con reductores como el coque, se reducirá para rechazar los metales interesantes de la escoria al metal. Este paso adicional también permite perfeccionar la decantación de la escoria. Sin este tratamiento de escoria, en la metalurgia del níquel, la recuperación de níquel es del 95 % (frente al 98 % en un horno eléctrico); para el cobre, del 80 al 93 %; y para el cobalto, del 26 al 70 %.[17] El horno flash de Inco puede, sin embargo, producir escorias menos ricas en cobre, evitando así el paso de decantar la escoria en un horno eléctrico.[E 6]
Sin embargo, en la metalurgia extractiva del cobre, algunas fundiciones empujan la oxidación hasta el punto de quemar todo el azufre contenido en la mata, con el fin de hacer innecesario su afinado en un convertidor Peirce-Smith (proceso Manhès-David).[E 1]
Notas
editar- ↑ Patentes inglesas n° 1131 de 21 de marzo de 1878, n° 4549 de 9 de noviembre de 1878 y otras.[3]
- ↑ A modo de comparación, a principios del siglo XX, la eficiencia térmica de un alto horno alcanzaba el 70 %, frente al 25 % de los hornos de reverbero equipados con regeneradores como los que se utilizaban en los hornos Martin-Siemems[9].
- ↑ Además del gran número de reacciones físico-químicas simultáneas que son propias del alto horno, cabe señalar que es fundamentalmente un horno de reducción-fusión y que es delicado convertirlo en un horno de oxidación-fusión. La combustión del coque produce monóxido de carbono, un gas muy reductor, mientras que el objetivo es oxidar la mayor cantidad posible de azufre y hierro para ahorrar combustible.
- ↑ Este horno costó unos 30 millones de dólares de 2010, es decir, el 12 % de los ingresos de Outokumpu.[8]
- ↑ En 1945, Inco realizó una cifra de negocios de 1480 millones de dólares de 2010, con 1480 millones de ganancia. En el mismo año, la facturación de Outokumpu alcanzó 105,3 millones de dólares de 2010, con 15,3 millones de beneficio. Inco suministraba el 90% de la demanda de níquel de occidente, mientras que Outokumpu suministraba del 1 al 2% del mercado occidental de cobre.[8]
- ↑ El oxígeno que vende Air Liquide finalmente cuesta la mitad del carbón que consumiría un horno de reverbero de idéntica capacidad.[14]
- ↑ Inco demostró que con el calor recuperado de una tonelada de nitrógeno presente en los humos, es posible fundir una tonelada de mineral.[1]
- ↑ El punto de fusión del FeO es 1377°C. Si FeO no se combina inmediatamente con sílice para formar fayalita (Fe
2SiO
4)[21] cuyo punto de fusión es 1208 °C, continúa su oxidación y se convierte en Fe
3O
4. ¡Pero el punto de fusión del Fe
3O
4 es de 1597°C! El Fe
3O
4 se aglomeraría en una masa sólida que evita el soplado y no se puede evacuar del horno,[22] si no fuera por el uso de fundentes reductores, tales como el hierro de espejo.[23]
Otra razón para combinar FeO con SiO
2 es que una escoria rica en óxidos de hierro puede oxidar Cu
2S siguiendo la reacción:- FeO
(laitier)+ Cu
2S
(matte)→ FeS
(matte)+ Cu
2O
(lechada)
- Tal reacción es indeseable porque hace que el cobre migre de la mata a la escoria. Por esta razón, los metalúrgicos evitan producir matas con más del 60% de cobre, aunque las ventajas de procesar una mata rica son obvias.[E 8]
- FeO
Referencias
editar- Schlesinger, Marc E.; King, Matthew J.; Sole, Kathryn C.; Davenport, William G. I. (2011). Elsevier, ed. Extractive Metallurgy of Copper (en inglés) (5 edición). p. 455. ISBN 978-0-08-096789-9.
- Otras referencias
- ↑ a b c d PdfOutokumpu (ed.). «Outokumpu Flash Smelting» (en inglés). Archivado desde el original el 24 de julio de 2011. Consultado el 22 de abril de 2022.
- ↑ a b c d e Sohn, H. Y.; Olivas-Martinez, M. (2014). «686-688». En Elsevier, ed. Treatise on Process Metallurgy (en inglés) 3 (A). p. 1745. ISBN 978-0-08-100000-7.
- ↑ a b Hollway, John. «Production of sulphur, copper matte, etc. from pyrites (patent US 234129 A)» (en inglés).
- ↑ 560-573. «Métallurgie : bessemérisation du cuivre». Bulletin de la Société de l'Industrie Minérale. 3 XV. 1920.
- ↑ Southwick, Larry M. (2008). «William Peirce and E.A. Cappelen Smith and Their Amazing Copper Converting Machine». En The Mineral, Metals & Materials Society (TMS), ed. JOM (en inglés) 60 (10).
- ↑ Peters, Edward Dyer (1905). «528». En The Engineering and Mining Journal, ed. Modern copper smelting (en inglés) (7 edición).
- ↑ Levy, Donald M. (1912). «192-193». En C. Griffin & company, limited, ed. Modern copper smelting (en inglés).
- ↑ a b c d e f g h i j k l m n ñ Korhonen, Janne M.; Välikangas, Liisa. «Constraints and Ingenuity: The Case of Outokumpu and the Development of Flash Smelting in the Copper Industry» (pdf) (en inglés). Archivado desde el original el 3 de marzo de 2016. Consultado el 22 de abril de 2022.
- ↑ Turner, Thomas (1908). «384». En C. Griffin & company, limited, ed. The Metallurgy of Iron: By Thomas Turner… [Being one of a series of treatises on metallurgy written by associates of the Royal school of mines]. Griffin's metallurgical series (en inglés). isbn2: 978-1177692878 (3 edición). p. 463. ISBN 1-177-69287-2.
- ↑ Bridgman, Henry L. «Process of reducing ores (patent US 578912 A)» (en inglés).
- ↑ Klepinger, John H.; Krejci, Milo W.; Kuzell, Charles R. «Process of smelting ores (patent US 1164653 A)» (en inglés).
- ↑ Freeman, Horace. «Process of smelting finely divided sulphide ores (patent US 1888164 A)» (en inglés).
- ↑ Newton, Joseph; Wilson, Curtis L. (juin de 1942). «161». En John Wiley & Sons, ed. Metallurgy of Copper (en inglés).
- ↑ a b c d Queneau, Paul E.; Marcuson, Samuel W. (1996). «Oxygen Pyrometallurgy at Copper Cliff—A Half Century of Progress». The Minerals, Metals & Materials Society (en inglés).
- ↑ a b Blazy, Pierre; Jdid, El-Aid. «Pyrométallurgie et électroraffinage du cuivre - Pyrométallurgie». En Éditions techniques de l'ingénieur, ed. Techniques de l'ingénieur (en francés).
- ↑ a b c d e PdfDirection régionale de l'environnement, de l'aménagement et du logement, ed. (décembre de 2001). «100-102». Document de référence sur les meilleures techniques disponibles [Industrie des métaux non ferreux]. p. 778. Archivado desde el original el 29 de abril de 2016. Consultado el 22 de abril de 2022.
- ↑ a b c d e f Krundwell, Frank K.; Moats, Michael S.; Ramachandran, Venkoba; Robinson, Timothy G.; Davenport, William G. (2011). «215 - 225». En Elsevier, ed. Extractive Metallurgy of Nickel, Cobalt and Platinum Group Metals (en inglés). p. 610. ISBN 978-0-08-096809-4.
- ↑ «The KIVCET Smelting Process» (en inglés). Aoüt de 2015.
- ↑ Davenport, William G. I.; Partelpoeg, Eric H. (1987). «295». En Pergamon Press, ed. Flash Smelting [Analysis, Control and Optimization] (en inglés). ISBN 0-08-034925-0.
- ↑ Davenport y Partelpoeg, 1987, p. 8
- ↑ Hofman, Heinrich Oscar (1914). «323». En MacGraw Hill Book Company, ed. Metallurgy of copper (en inglés).
- ↑ Krundwell et al., 2011, p. 127
- ↑ Hofman, 1914, p. 342
- ↑ Stojanović, Nenad M; Milić, Marko Kimi; Milošević, Darko M (2014). Implementation of modern technologies in metallurgy in the function of protection of the environment and natural ressources (pdf) (en inglés). ISBN 978-86-7747-486-7.